Products
Pusher centrifuge
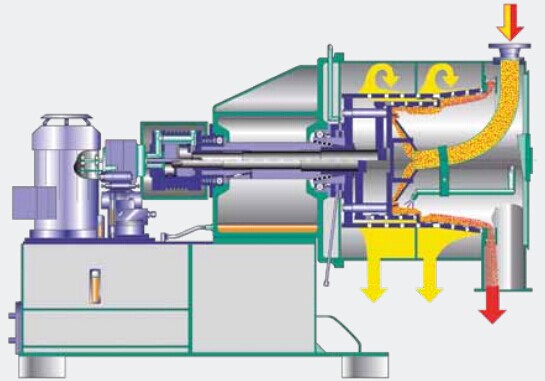
In the pusher centrifuge, the sliding speed of solid particles in the slot screen is lower than that in the spiral screen centrifuge. Therefore, the residence time of the material in the sieve basket is also longer, and the filter cake formed is relatively thick. Therefore, the pusher centrifuge is especially suitable for processing products with high wear. The thick filter cake layer makes the subsequent materials not in direct contact with the screen, reducing the wear of the product to the screen.
Sieve Deli pushing centrifuge series includes single-stage, two-stage and three-stage rotating parts. In most applications, the outer side of the maximum diameter sieve basket adopts the cone basket design. This design makes the original thick filter cake become loose, and with the continuous increase of diameter, the centrifugal force becomes larger, the thickness of filter cake becomes smaller, and it is easier to dehydrate. Another advantage of the cylindrical / conical basket design of the single-stage rotating part of the pusher centrifuge is that it reduces the energy consumption of pushing solids in the process of conveying solids.
Single stage pusher centrifuge is the most economical solution for simple separation. The so-called simple separation refers to the separation of crystalline solids with large particle size from the slurry with high solid concentration. In various applications, two-stage pushing is the most used. The two-stage pusher centrifuge is more widely used than the single-stage pusher centrifuge, mainly because the screen baskets at all levels are relatively short. Feeds with varying solid concentrations or finer particles can also be handled more easily. At the same time, the separation and discharge of mother liquor and cleaning liquid can also be realized more easily. The three-stage pusher centrifuge is applicable to the mother liquor of materials with high viscosity or requiring independent one-stage cleaning
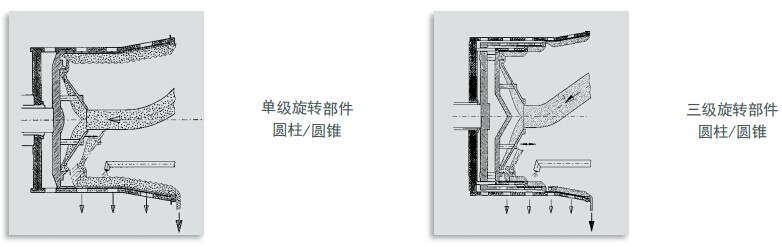
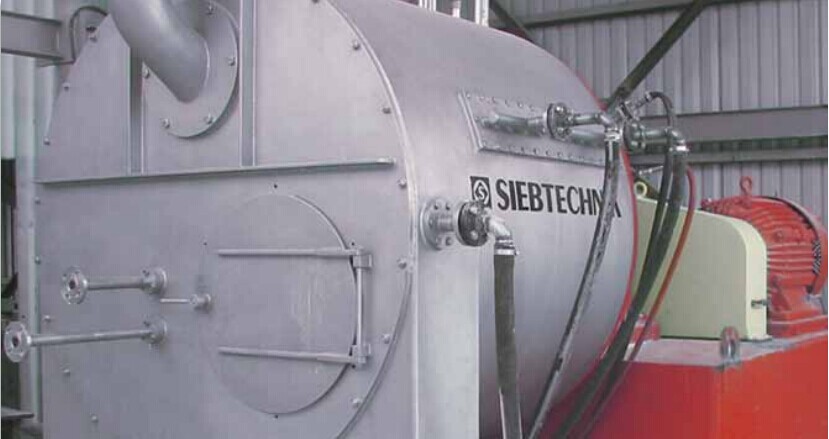
Sieve Deli pushing centrifuge is divided into:
N process area
N bearing lubrication system
N hydraulic pushing system
The rotating parts are placed horizontally so that it is easy to access the process area and driving parts. Considering the standards of equipment processing and operation, the equipment is designed according to the system unit.
In addition to the base, the basic part also includes:
N pump (including hydraulic control)
N pressure switch and thermometer
N bearing
N drive of rotation and pushing
The base is divided into two chambers. The first chamber is used as the oil tank for storing lubricating liquid or coolant. The second chamber is used to store concrete fragments for counterweight to stabilize the base.
An elastic damping component is installed under the centrifuge base. The product room is mounted on the base by cantilever. The product room is divided into filtrate discharge area and solid discharge area. The cantilever structure is also used for rotating parts.
The opening on the inner surface is the screen basket, and the direction of its long seam is parallel to the axis, that is, along the pushing direction.
The front cover plate of the product room is connected by bolts or hinges, which can facilitate the disassembly and assembly of vulnerable parts, such as screen basket, feed cone, etc.
The pushing part is realized by hydraulic system. Oil quantity and oil pressure are provided by screw pump driven by three-phase motor.
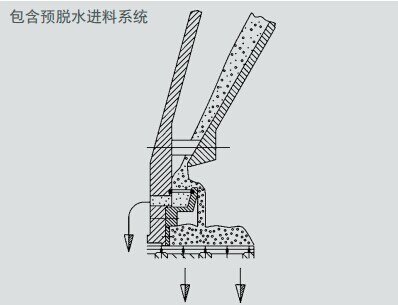
N the feed system includes pre dehydration design
N gas seal configuration, which can be treated with inert gas
N screw feeder can be used
N mother liquor and cleaning solution shall be discharged separately
N explosion proof performance in accordance with EU standards
N conform to the specifications of processed food
N other special configurations are provided according to user requirements
Working principle of two-stage pusher centrifuge
The mixture of solid and liquid continuously enters the distribution cone through the feed pipe, and the speed of the distribution cone is the same as that of the screen basket.
Here, the mixture is accelerated, flows through the annular gap between the bottom of the ejector and the distribution cone, and enters the screen by overflow. Most of the liquid is centrifuged through the sieve cone. The solid material is left on the screen surface as a filter cake. In addition to rotation, the screen basket performs axial reciprocating motion at the same time. In this process, the filter cake is gradually pushed to the open end of the screen basket by the pusher, enters the solid blanking area and leaves the centrifuge.
After washing the filter cake in the main dehydration area, the residual mother liquor in the filter cake can be washed away. The friction between the filter cake and the friction between the filter cake and the screen effectively determines the thickness of the filter cake. According to the size of the product and machine, its thickness is medium
Between 15mm and 80mm. The production capacity of pusher centrifuge mainly depends on the feed quantity. The newly formed filter cake must be dehydrated in a short time between two pushing strokes, and the pushing force is enough to push and disperse the filter cake already formed in the screen basket. The higher the solid content of the feed, the higher the corresponding output.
Standard technical parameters
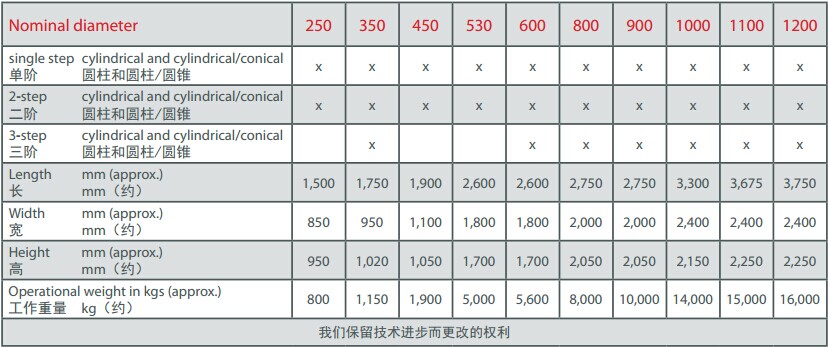
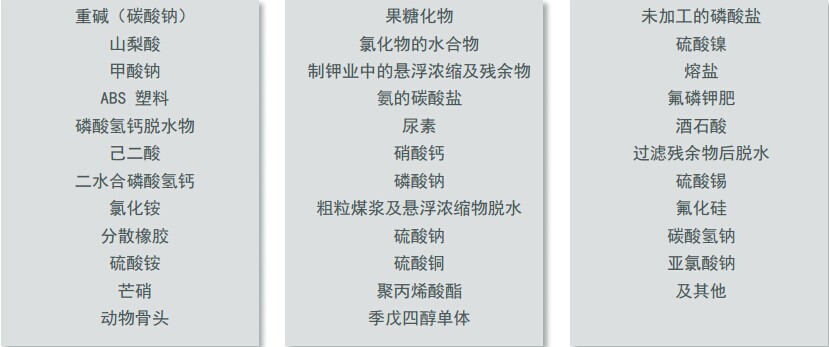