Products
Double cone sedimentation centrifuge
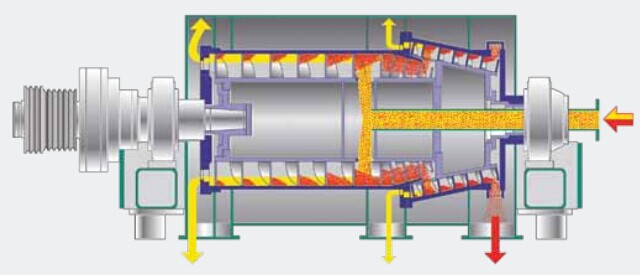
Sedimentation centrifuge uses mechanical method to dehydrate small and incompressible solids. The most important design index is the dryness of solids. Better dewatering effect can be achieved by using double cone sedimentation centrifuge. The slurry entering the feed pipe is accelerated in a drum with a relatively small diameter that meets the clarification requirements, and the small diameter has low energy consumption for acceleration. The solid material in the clarifier becomes thicker in the primary cone section (the first cone in the double cone sedimentation machine). The liquid level in the settlement section can be changed by adjusting the overflow plate without affecting the drying of the cone section. The precipitated thickened solid is moved from the primary cone to the secondary cone with larger diameter. The filter cake is reoriented, broken and redistributed here. This reduces the thickness of the filter cake and is conducive to dehydration.
In addition, the diameter of the secondary cone section is larger, which can produce greater centrifugal force at the same speed. This separates the residual moisture from the solid material. The separated liquid is regulated by another adjustable overflow plate. The liquid discharged through the liquid discharge port of the secondary cone section may take away a small amount of solid materials, which can be sent back to the feed pipe for continuous separation (repeated circulation without loss of solid materials). If necessary, the solid material can be flushed in the secondary cone section. The flushing solution can be kept separated from the mother liquor
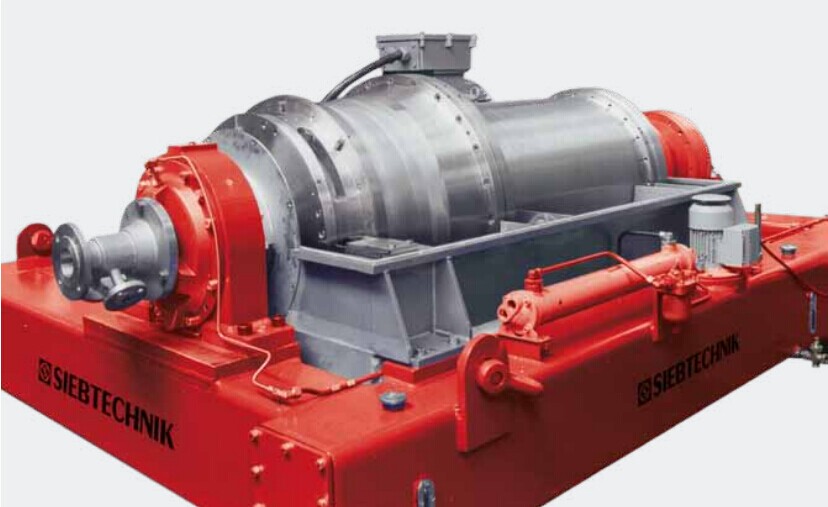
N clarification and drying are carried out in two separately designed drum devices with different proportions;
N the liquid level of clarification section and drying section can be adjusted respectively;
N the solid load between helical blades allows the liquid to flow freely and eliminates the influence of the solid movement pushed forward by the spiral. This requires the use of the proven heavy-duty cyclo differential to ensure the speed difference between the drum and the screw;
N the filter cake thickens in the primary cone section, and then is broken up when entering the secondary cone section to form the filter cake again;
N the second stage cone has larger capacity, the filter cake becomes thinner and the load on the screw is lower;
N in the secondary cone, the centrifugal force is greater, which is conducive to dehydration;
N use a drum with smaller diameter to separate a large amount of liquid, because under certain acceleration conditions, the diameter is directly proportional to the square of the required power, so significant energy-saving effect can be obtained;
N in the secondary cone section, the flushing liquid and mother liquor can be discharged separately, and whether to flush or not can be optional;
N during shutdown and deceleration, the liquid will not be brought into the solid discharge area from the primary cone section.
Standard technical parameters
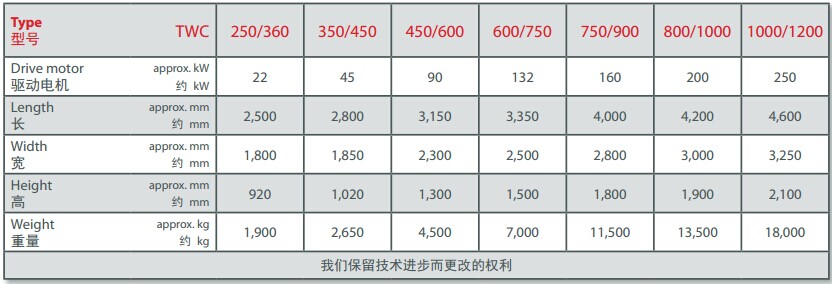
Successful application cases
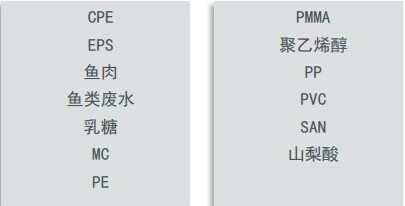