Products
Spiral screen centrifuge
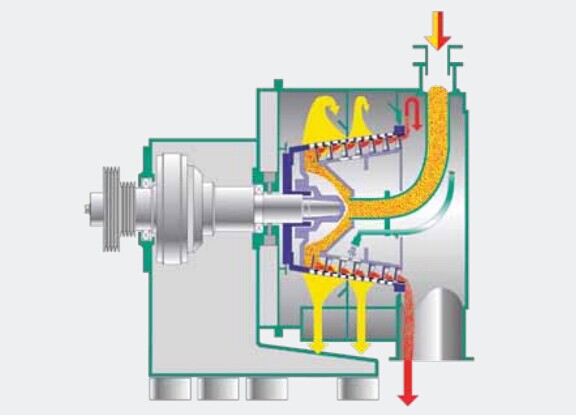
brief introduction
Among the continuous centrifuges we produce, the most common is the spiral screen centrifuge. In this machine, the solid particles left on the screen are transmitted from small diameter to large diameter through the inclination angle of the screen basket and the speed difference between the spiral scraper and the screen basket. For different feeds, sieve baskets with different inclination angles can be selected. Various products, such as short fiber cotton wool, freeze concentrated crystals or granular plastics, can be successfully separated from the mother liquor and cleaned if necessary. According to the operating conditions, mechanical stamping screen or slotted screen can be used.
The transmission of centrifuge is realized by belt pulley and V-belt,
To meet the process requirements. Cyclo-gearbox can ensure the required speed difference between the spiral scraper and the screen basket to ensure the performance of the centrifuge.
The overload protection of centrifuge is realized by clutch. Except that H200 has an oil immersed gearbox, the gearbox and bearings of other models are lubricated by the lubrication system driven by the oil pump motor. The machine and the drive motor are installed on the base, and the vibration is isolated through the rubber damping components fastened with the support structure. Even our largest centrifuge cx1500 can be installed without special foundation. After the equipment is shut down, the differential speed will remain for a short time, and the relative movement of the spiral scraper and the screen basket will remove the residual solids left on the screen basket.
Material properties
According to the contact with materials, the parts can be made of stainless steel, Hastelloy, nickel based heat and corrosion resistant alloy, nickel, titanium or similar materials. For parts prone to surface wear, wear-resistant materials shall be used for protection.
Special configuration
The working chamber is sealed with:
-Labyrinth gas seal;
-PTFE ring seal;
-Sliding ring seal.
Cyclone separator (available),
Return the gas in the circulating tank to the solid particle device
Blanking ring with discharge scraper
Screw feeder
Mother liquor and flushing liquid are discharged separately
Other devices customized for special requirements of users
classification
1. H series
In the traditional H series, the whole rotating part is installed on a large bearing pedestal. The screen basket and spiral scraper extend cantilevered to the product room. The bearing pedestal is also used as the base of the equipment and integrates the lubricating oil tank and drive system.
The product room is installed at the front end of the bearing pedestal through a large diameter flange. In design, the bearing seat is the main support of the whole equipment.
Among the continuous centrifuges we produce, the most common is the spiral screen centrifuge. In this machine, the solid particles left on the screen are transmitted from small diameter to large diameter through the inclination angle of the screen basket and the speed difference between the spiral scraper and the screen basket. For different feeds, sieve baskets with different inclination angles can be selected. Various products, such as short fiber cotton wool, freeze concentrated crystals or granular plastics, can be successfully separated from the mother liquor and cleaned if necessary. According to the operating conditions, mechanical stamping screen or slotted screen can be used.
The transmission of centrifuge is realized by belt pulley and V-belt,
To meet the process requirements. Cyclo-gearbox can ensure the required speed difference between the spiral scraper and the screen basket to ensure the performance of the centrifuge.
The overload protection of centrifuge is realized by clutch. Except that H200 has an oil immersed gearbox, the gearbox and bearings of other models are lubricated by the lubrication system driven by the oil pump motor. The machine and the drive motor are installed on the base, and the vibration is isolated through the rubber damping components fastened with the support structure. Even our largest centrifuge cx1500 can be installed without special foundation. After the equipment is shut down, the differential speed will remain for a short time, and the relative movement of the spiral scraper and the screen basket will remove the residual solids left on the screen basket.
Material properties
According to the contact with materials, the parts can be made of stainless steel, Hastelloy, nickel based heat and corrosion resistant alloy, nickel, titanium or similar materials. For parts prone to surface wear, wear-resistant materials shall be used for protection.
Special configuration
The working chamber is sealed with:
-Labyrinth gas seal;
-PTFE ring seal;
-Sliding ring seal.
Cyclone separator (available),
Return the gas in the circulating tank to the solid particle device
Blanking ring with discharge scraper
Screw feeder
Mother liquor and flushing liquid are discharged separately
Other devices customized for special requirements of users
classification
1. H series
In the traditional H series, the whole rotating part is installed on a large bearing pedestal. The screen basket and spiral scraper extend cantilevered to the product room. The bearing pedestal is also used as the base of the equipment and integrates the lubricating oil tank and drive system.
The product room is installed at the front end of the bearing pedestal through a large diameter flange. In design, the bearing seat is the main support of the whole equipment.
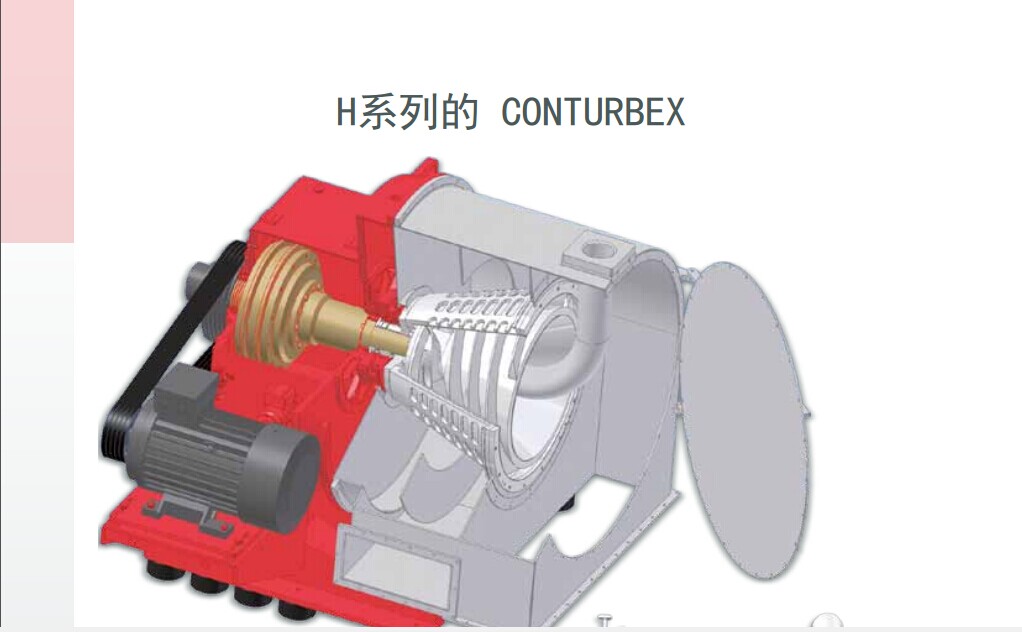
H series parameters
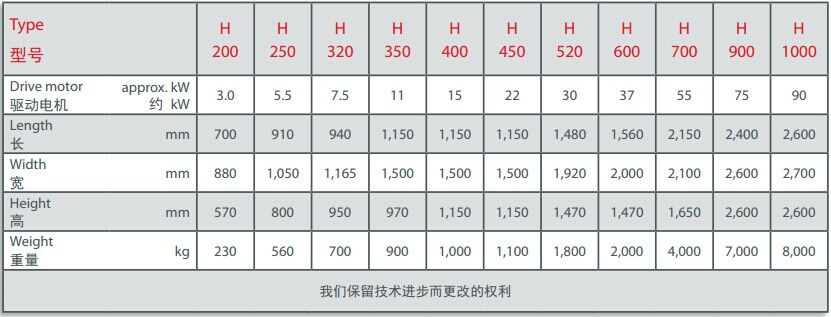
2. CX series
CX series is the latest design. Compared with the traditional H series, there are only more than 20 main components, which can be divided into four parts:
N base
N rotating parts with differential
N product room
N lubrication system
The simplified rotating parts and differential are self centering, which can ensure the correct positioning of the central shaft, independent of the product room, and optimize the operation performance. This simplified design not only makes the driving components simpler, but also allows users to store only a small amount of spare parts.
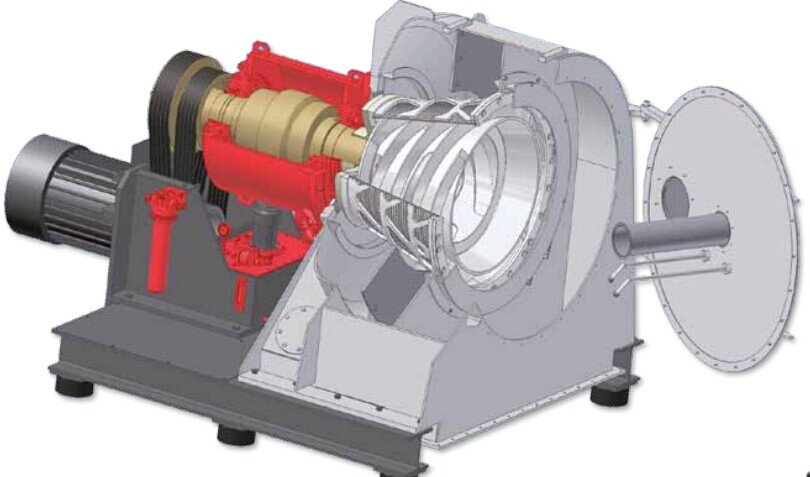
CX series parameters
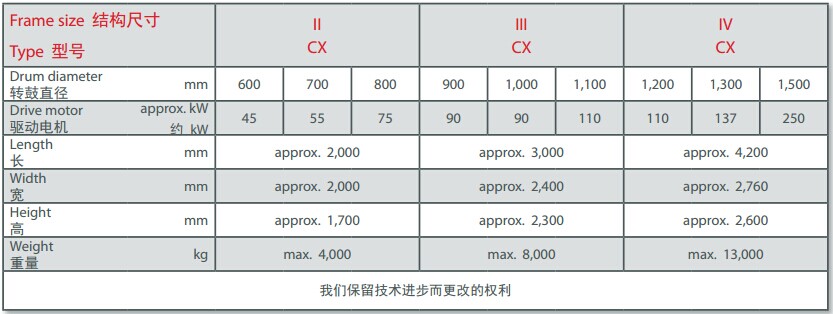
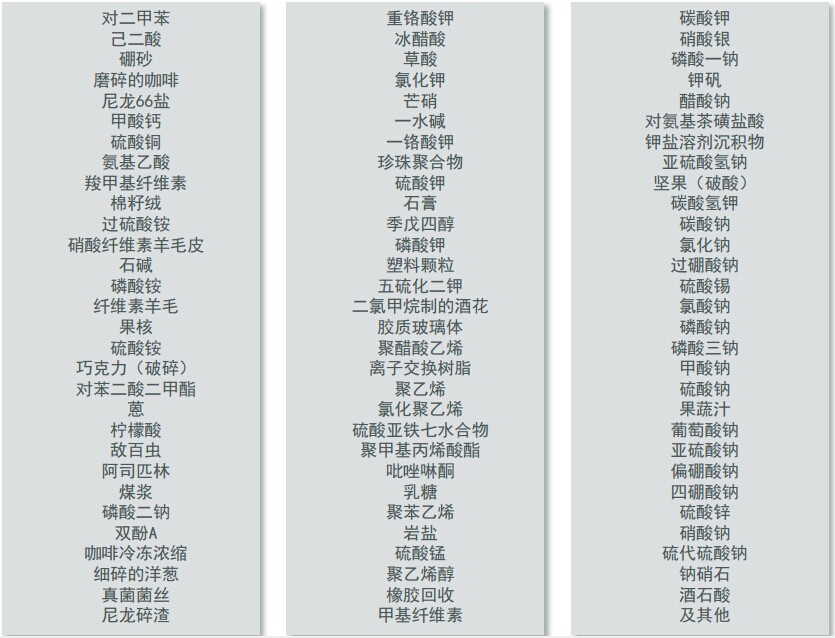
For many processes and products, conturbex is equipped with a variety of components to meet the special use requirements of customers. Whether airtight or non airtight process, there are corresponding design and full matching.
The inclination angle of the screen basket can be adjusted according to the product and the work
Adjust the following:
n 0°- 20°
Selection of various screens:
N wedge screen
N conidur screen
N laser screen
Three drive designs:
N cyclo gearbox
Siebink planetary drive
N hydraulic drive (variable worm speed).
It can support two drive motors (screen barrel and worm)
The transmission can regulate the speed
The following design can be carried out according to the requirements of process sealing:
N open labyrinth seal
N PTFE seal for vapor tight design
N PTFE seal for airtight design
N slip ring seal with pressure tight design
Material design
Centrifuge in contact with product materials according to different purposes
All parts are made of corrosion-resistant austenitic steel, Hastelloy, nickel steel or stainless steel
Made of titanium steel, etc.
Machines used in coal and sand industries are made entirely of carbon steel.
For hard products with wear, the machine adopts anti-wear materials
Special surface made of.
CIP cleaning
According to the standard, all conturbex centrifuges are equipped with cleaning equipment
Nozzle to clean up residual products in the equipment.
If there are higher requirements for the machine, CIP system can also be installed,
Including special flushing pipe, special nozzle and slow drive program.
ATEX design of explosion-proof area
All sieve centrifuges are available in accordance with EU directives
The ATEX explosion-proof system is installed according to the standard of 94 / 9 / EC (atex100a),
To meet the work requirements in hazardous areas.
Type selection information:
1. Solid liquid mixing ratio of materials
2. Viscosity of materials;
3. Normal distribution of crystal particle diameter;
4. The amount of centrifugal material required every day;
5. Physical properties of materials;
6. Chemical properties of dry materials and solvents;
7. Recovery of solid phase materials or liquid phase materials;
8. Centrifuge placement space and environment.